Factory, Foaming Process, Raw Materials, Foaming Agents
The basics of foamglass manufacturing.
Factory
Foamglass manufacturing requires high temperatures. Therefore the it's usually designed as an ongoing, 24/7, process. Every step of the process can be automated to a level with minimal manual handling needed within the factory.
Desired Final Product
- Foamglass Gravel
- Foamglass Block
- Foamglass Granulate
What is the product you're aiming to manufacture?
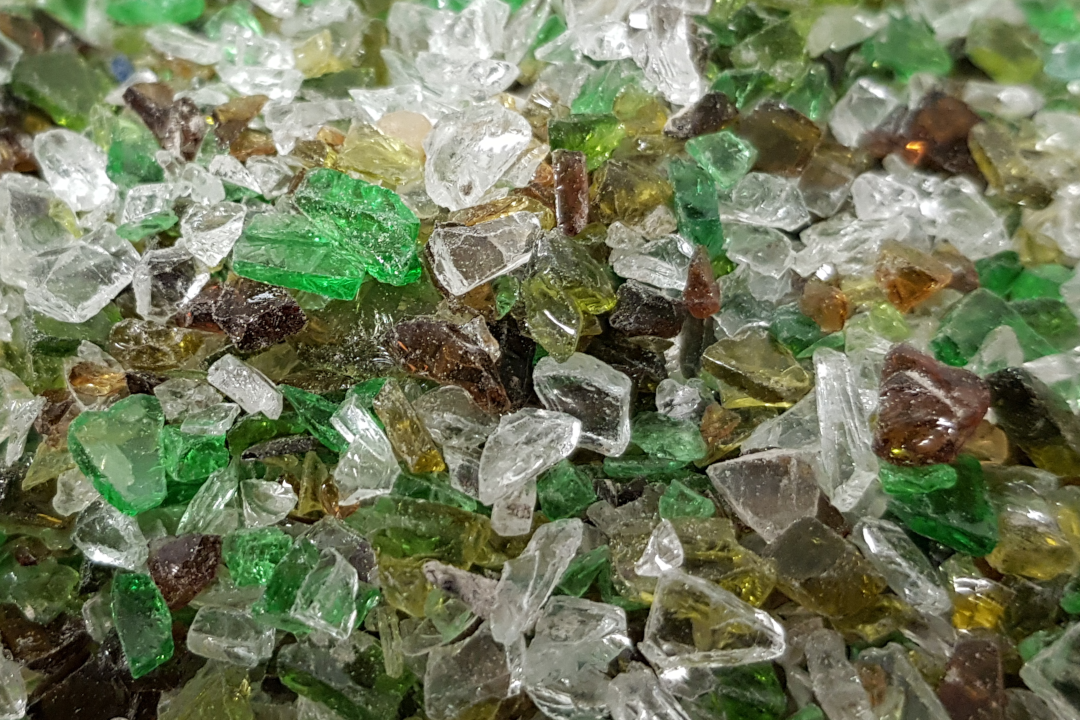
Raw Materials
Glass
You need an access to glass (recycled, cleaned glass or glasspowder).
Glass cullet must be grinded down to powder.
The grain size distribution of the powder and the purity of the glass plays an important part in the foaming process.
Suitable Foaming agents described in the Foaming Process -section.
Preparing the glass for Foaming Process: [Gravel, Dry]
Properties of Raw Materials
Depending on your glass source quality, you may need to conduct pre-testing and planning of the infeed mix of materials.
Tests may include: Color classification, LOI, CSP degree.
Drying
In a typical process, the glass has to be dried before milling.
Drying processes often offer a possibility of also separating organic impurities from the raw materials.
Crushing
Crushing might be needed to achieve a capable milling process, depending on size distribution of the raw glass.
Optimal size distribution for milling is dependent of the Milling solution used.
Milling
Final step of powder making. Variety of options to achieve powder fine enough exists.
Possible solutions: Rod Mill, Ball Mill.. with sieving or air classification.
Testing of Powder Properties
Testing of grain size should be conducted, to ensure the process performance and to find possible faults in the milling system.
Possible testing for impurities may also be needed.
Foaming Process: [Gravel, Dry Process]
Mixing
For the production of foam glass, a basic raw material, e.g. glass powder and a foaming agent, e.g. silicon carbide, glycerin or technical coal and in case of liquid components a stabilizer, e.g. sodium waterglass is required.
(The worse the quality of the glass powder, the more important becomes the use of a stabilizer)
Drying
After mixing the raw materials, they are fed onto the conveyor belt. In the first zones of the kiln the mixture dries.
Sintering
During sintering, the powder particles "stick" together and form a solid cake with millions of small, and homogeneously distributed closed cells.
If the temperature in the furnace is now increased, chemical reactions form the foaming gas take place and the pressure inside the bubble increases.
(The temperature increase causes a reduction in glass viscosity.)
Foaming
Foaming of the cake occurs when the pressure in the bubble exceeds the viscosity dependent resistance of the glass.
The following parameters influence the foaming process:
- Particle size distribution of the glass powder.
- Purity of the glass and constancy in glass quality: recycled glass is less suitable than specially melted glass.
- Oxidation state of the glass: the higher the concentration of chemically dissolved oxygen in the glass, the better.
- Quality and homogeneous distribution of the foaming agent: the more homogeneous the distribution, the better.
- Temperature control in the tunnel furnace)
Cooling
At the end of the process, the continuous form ribbon breaks down into gravel pieces of 10 – 60 mm.
No waste is produced.
Gravel Foaming process in short:
First the glasspowder and additives are combined together; Mixing. Ready mixture is fed inside the production kiln where in the first phase the mixture is Dried. In Sintering phase the powder particles 'stick' together forming a solid cake with huge amount of closed cells. As the temperatures are rised the mixture of additive(s) and gases inside the glass form foaming gases inside the cells which expand as the pressure rises over the resistance of cells. After the foaming the product is cooled down slowly to hold the form gained from foaming to the point of breaking naturally into gravel pieces.
Gravel Production from Powder to Transport:
Foamglass Blocks, Granulates or Gravel in Wet Process.
For more information, see below!